Just-in-time manufacturing - Definition, example, pros, and cons
Learn everything about just-in-time manufacturing - definition, how it works, how to implement it, tool to manage it, and pros and cons, and more.
by OneAdvanced PRPublished on 22 January 2025 6 minute read
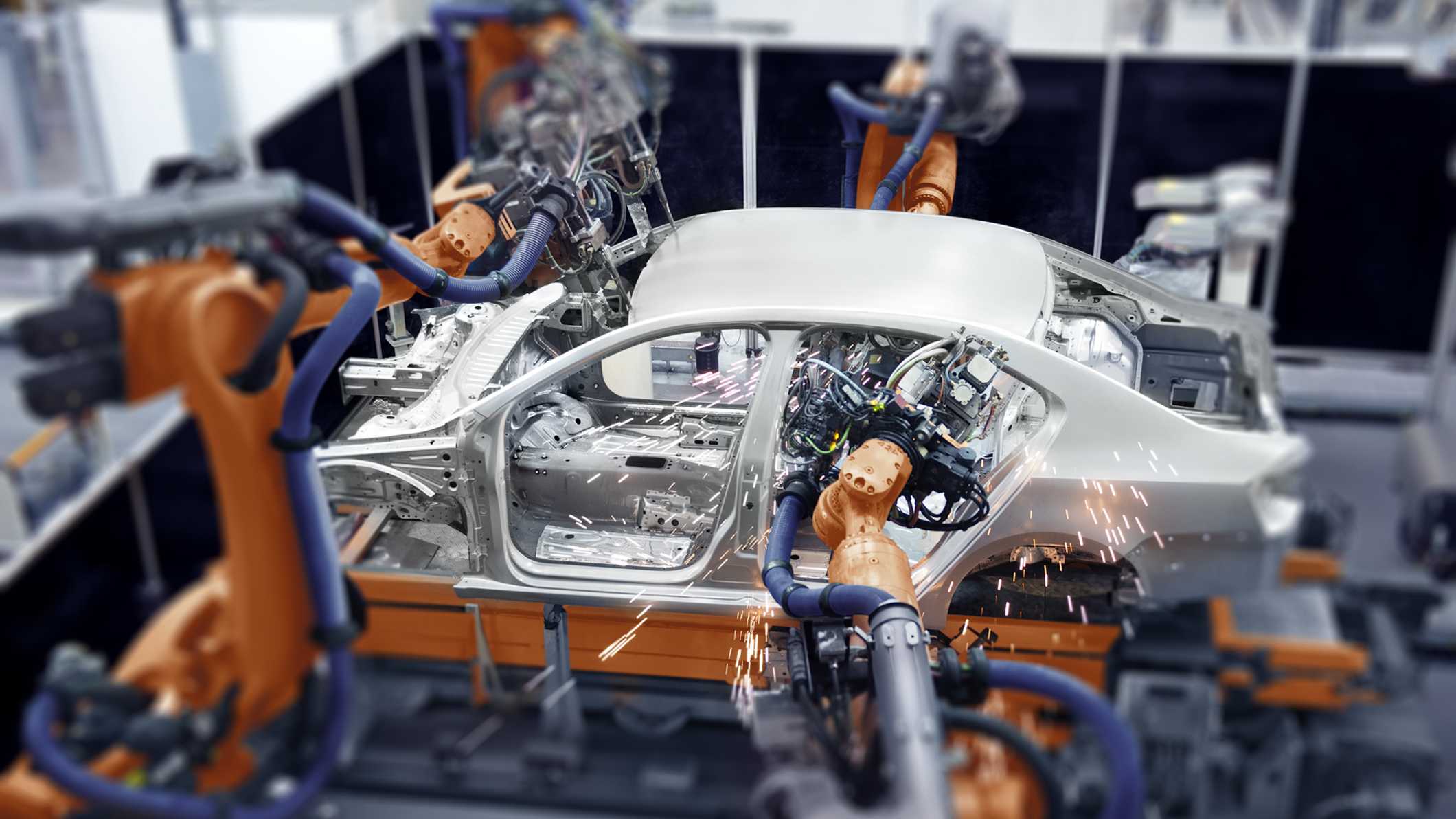
What is Just-in-time manufacturing?
Just-in-Time (JIT) Manufacturing is a manufacturing strategy aimed to improve the efficiency of businesses and reduce their material waste by aligning production to customer demand. This approach ensures that materials are ordered and received only when they are needed in the production process. JIT requires companies to forecast demand accurately and maintain a successfully managed supply chain. By utilising materials "just in time”, organisations can cut storage costs, reduce overproduction, and streamline processes, fostering a more efficient manufacturing environment.
Example of Just-in-time manufacturing
A classic example of JIT is Toyota's production system. The car manufacturer implemented this model to produce parts only when necessary, aligning inventory orders with customer demand. The system streamlined operations, enhanced efficiency, and minimised waste.
In 1997, however, Toyota’s reliance on JIT was tested when a fire appeared at its sole supplier Aisin, which made P-valves for the company. The result was halted production, and it disrupted production for days. It cost the company over 160 billion yen of their revenue. This incident shed light on both the positives and negatives of the JIT approach.
How does JIT manufacturing work?
Here’s a brief explanation of how JIT works:
- Manufacturers produce goods based on confirmed orders, avoiding surplus.
- Companies rely on strong supplier relationships to receive materials promptly.
- Processes are optimised to ensure smooth workflows without delays.
- Tools like Kanban help maintain steady production and reduce overcapacity.
For instance, an electronics manufacturer might order parts for assembly only once a customer places an order. This reduces storage costs, limits waste, and maximises efficiency – all while meeting customer requirements on time.
How to implement Just-in-time production for manufacturing
Implementing a JIT production system requires strategic planning and commitment to change. Here’s a detailed breakdown of the key steps involved, along with insights into how each contributes to the success of the system:
1. Build strong supplier relationships
Establishing dependable relationships with suppliers is the backbone of a JIT system. Manufacturers should partner with suppliers who can deliver materials promptly, always aiming for smaller, frequent shipments.
- Why it matters: Dependable suppliers ensure that raw materials arrive exactly when needed, avoiding delays that could halt production.
- How to achieve it: Regularly communicate expectations, negotiate service-level agreements, and monitor supplier performance. Building trust and collaboration ensures smoother operations and minimal disruptions.
2. Standardise internal processes
Streamlining and standardising workflows helps to maintain consistency in production. When every process is well-documented and optimised, it reduces bottlenecks.
- Why it matters: Standardisation ensures that all operations align, supporting faster production cycles and more predictable outputs.
- How to achieve it: Conduct a thorough review of existing processes to identify inefficiencies. Implement clearly defined standard operating procedures (SOPs) and train staff to adhere to them.
3. Focus on waste reduction
A primary goal of JIT manufacturing is to minimise waste across all stages of production. This isn’t limited to physical materials; it also includes wasted time, labour, and unnecessary movement.
- Why it matters: Reducing waste lowers costs and ensures that resources are utilised effectively.
- How to achieve it: Use techniques like value stream mapping to identify inefficiencies. Incorporate tools to reduce defects and ensure right-first-time production quality.
4. Invest in communication and visibility tools
For JIT to run effectively, manufacturers need precise control and visibility over their supply chains and production schedules. Technology plays a key role here.
- Why it matters: Real-time data ensures teams can adapt quickly to changes or disruptions.
- How to achieve it: Invest in supply chain tools, and efficient inventory tracking solutions. These tools help monitor stock levels, track deliveries, and forecast demand with greater accuracy.
5. Plan for contingencies
Though JIT minimises inventory wastage, it can introduce some vulnerabilities to the supply chain. Having a backup plan ensures production continuity even when unexpected situations arise
- Why it matters: Without contingency planning, any disruption, such as supplier delays or transport issues, could bring production to a standstill.
- How to achieve it: Develop alternative supplier networks, maintain minimum safety stock for critical items, and establish protocols for managing disruptions. Additionally, run regular “what-if” scenarios to assess the resilience of your supply chain.
Pros and cons of Just-in-time manufacturing
Like most of the other manufacturing processes, JIT has both benefits and drawbacks. Here are some of the pros and cons:
Pros
Lower inventory costs: Materials are ordered only when needed, reducing the need for large storage facilities.
Faster production times: JIT enables streamlined production schedules, ensuring quicker order fulfilment.
Improved cash flow: Less money is tied up in raw materials and stock, boosting financial liquidity.
Reduced waste: By producing only what’s required, companies avoid waste from unsold or expired inventory.
Flexible production: JIT allows organisations to quickly adapt to market changes.
Better quality control: Early identification of defects ensures issues can be addressed before they escalate.
Better supplier relationships: Improves relationships with collaborative scheduling and timely deliveries, fostering trust and better communication with the supplier.
Cons
Supply chain dependency: Disruptions in the supply chain can bring production to a stop.
Potential delays: A sudden order increase or supplier failure may lead to production bottlenecks.
Higher per-unit costs: Purchasing smaller volumes may increase costs compared to bulk-buying.
Supplier limitations: Some suppliers may impose minimum order quantities, complicating Just-in-time practices.
Reduced quality oversight: Less scope for random quality evaluations can lead to overlooked defects in production.
Who should go for Just-in-time inventory in manufacturing?
The JIT inventory strategy offers significant advantages, but it is not suitable for every organisation. To ensure success, companies must meet specific conditions. Here’s a step-by-step guide on adopting the JIT manufacturing process:
Step 1: Assess your ability to forecast demand
Evaluate if your organisation can predict customer demand with accuracy. Businesses with access to reliable data and advanced forecasting tools will have a better chance of aligning production with actual needs. This minimises the risk of outcomes like stockouts.
Step 2: Evaluate supplier reliability
Find suppliers who are dependable and consistently deliver materials on time without affecting the quality. A solid partnership with trustworthy suppliers ensures a smooth flow of resources, essential for maintaining production efficiency.
Step 3: Consider industry risks
Analyse your industry for risks of sudden demand spikes or supply chain disruptions. JIT works best in sectors with stable and predictable demand, like furniture or packaging. High-risk businesses such as food or pharmaceuticals, may find JIT harder to implement.
Step 4: Review operational flexibility
Determine if your production processes can adapt quickly to changing circumstances. JIT thrives in environments with flexible production lines, versatile teams, and workflows that can scale up or down seamlessly.
Step 5: Commit to efficiency
Your organisation should commit to increasing productivity. Adopting lean manufacturing principles and continuous improvement strategies will ensure you maximise the benefits of JIT while reducing unnecessary costs.
Step 6: Test readiness
Conduct a pilot implementation of JIT in a controlled environment within your organisation. This allows you to identify potential challenges and fine-tune processes before a full-scale rollout.
Tools to support Just-in-time approach for manufacturing companies
OneAdvanced offers manufacturing software tailored to support lean manufacturing. These tools streamline supply chain management, enhance real-time visibility, and optimise production processes – everything a company needs to succeed with JIT. By reducing complexities and automating inventory tracking, our Cloud-based solutions empower manufacturers to focus on delivering high-quality products swiftly and efficiently.
FAQs
Who invented the Just-in-time method of production?
The JIT system or Kanban was pioneered by Toyota and credited to its industrial engineer Taiichi Ohno.
What type of waste does Just-in-time production reduce?
JIT reduces waste such as overproduction, excessive inventory, defects, and unnecessary transportation or energy emissions.
About the author
OneAdvanced PR
Press Team
Our dedicated press team is committed to delivering thought leadership, insightful market analysis, and timely updates to keep you informed. We uncover trends, share expert perspectives, and provide in-depth commentary on the latest developments for the sectors that we serve. Whether it’s breaking news, comprehensive reports, or forward-thinking strategies, our goal is to provide valuable insights that inform, inspire, and help you stay ahead in a rapidly evolving landscape.