SMART goals for manufacturing employees
This blog explores how manufacturing leaders and employees can leverage SMART goals to drive individual growth and contribute to organisational success.
by OneAdvanced PRPublished on 15 October 2024 3 minute read
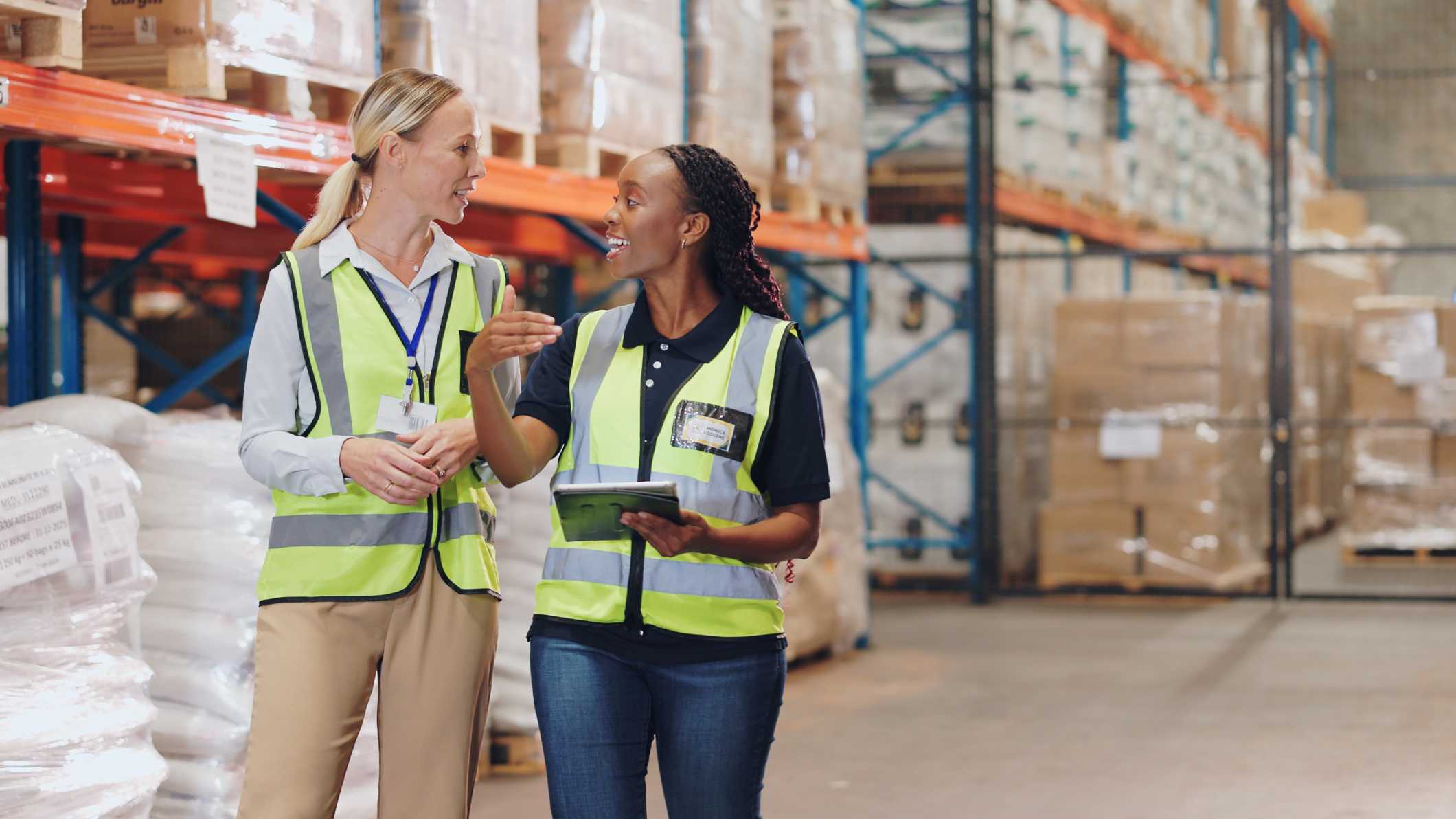
A recent report revealed a disconnect between managers and employees in the manufacturing industry: in 2024, 91 percent of managers indicated that their companies are prioritising upskilling, but only 70 per cent of workers agreed. This suggests that performance enhancing initiatives are being decided at a high level, but are not being understood and followed through on the frontline.
Engaging workers in professional development and upskilling requires overarching strategy, dedicated resource and time investment. One key piece of the puzzle is setting SMART goals. Specific, measurable, achievable, relevant, and time-bound objectives provide clarity and direction, ensuring every team member understands their role in the bigger picture – reducing the risk of upskilling initiatives becoming lost or misunderstood.
This blog explores how manufacturing leaders and employees can leverage SMART goals to drive individual growth and contribute to organisational success.
Why manufacturing needs SMART goals
SMART goals are a game-changer in any industry, but they hold particular importance in manufacturing, where frontline workers are at risk of feeling unengaged and churn rates are high; Make UK’s labour turnover report reveals that employee attrition is 10 per cent higher in manufacturing than industry averages. To keep workers in their jobs, its vital to show them they have a future both in their current role and the sector, mapping out a clear professional development path. Vague goals, where the value is not clear, or worse, no development objectives at all, risk the workforce feeling despondent and unmotivated to succeed.
By breaking down complex targets into manageable tasks, SMART goals provide a clear roadmap for employees. This clarity fosters motivation and accountability, as team members can easily track their progress and know exactly what's expected of them.
How to create SMART goals
Specificity: Define clear objectives
The first step in setting SMART goals is to be specific about what you want to achieve. This means identifying concrete objectives, with clear outcomes.
For example, if you're aiming to reduce production downtime, define the exact target, such as lowering machine idle time by 20 percent, and then create individual goals that help to achieve this aim – like setting objectives towards making sure machines are turned off when not in use and designing efficient work days.
Measurability: Track progress with precision
Measuring progress is a critical component of SMART goals. This involves establishing key performance indicators (KPIs) and regularly monitoring performance against these metrics.
For instance, if your goal is to increase output, set a measurable target such as producing 100 units per hour. Use data-driven tools and techniques to track progress, such as real-time monitoring systems or quality control checks.
Relevance: Align goals with business objectives
SMART goals should always be relevant to both an individual’s role and career progression, and the broader business objectives. This means aligning individual goals with the company's strategic priorities.
Consider how each goal contributes to the overall success of the organisation. For example, if you're focused on reducing waste, ensure that this aligns with the company's sustainability initiatives.
By matching goals to business objectives, you create a sense of purpose and meaning. Employees understand the impact of their efforts and are motivated to contribute to the company's success. This alignment fosters a culture of collaboration and shared responsibility
Time-bound: Set deadlines for accountability
Setting a deadline for achieving goals is a crucial aspect of SMART goal setting. Determine the timeframe within which the goal should be achieved. It could be a weekly, monthly, or quarterly target, depending on the complexity of the task.
By setting deadlines, you create a sense of urgency and accountability. Employees are motivated to complete tasks efficiently and avoid procrastination. This time-bound approach ensures that progress is made consistently, driving momentum and delivering results.
SMART goals are a powerful tool for manufacturing employees, providing clarity, direction, and motivation. Find out more about how to improve your performance management process in our latest guide, 10 ways to modernise performance management.
About the author
OneAdvanced PR
Press Team
Our dedicated press team is committed to delivering thought leadership, insightful market analysis, and timely updates to keep you informed. We uncover trends, share expert perspectives, and provide in-depth commentary on the latest developments for the sectors that we serve. Whether it’s breaking news, comprehensive reports, or forward-thinking strategies, our goal is to provide valuable insights that inform, inspire, and help you stay ahead in a rapidly evolving landscape.